Jeevika Food Machinery Co., Chennai is a dynamic company founded with the motivation to provide added value goods and services to Indian food processing industries such as: rice industry, pasta industry, dal industry, wheat industry, maize industry, nuts industry, dry fruits industry, snacks industry, confectionery industry, spice industry, frozen fruits & vegetable industry, dehydrated vegetable & fruits industry, salt industry, sugar industry and ready to eat food industry.
Jeevika Food Machinery Co., India is exclusively dealing the food & snacks processing machineries such as: Optical Color Sorter Machine, Innovative Sorting Solutions, Quality Inspection System, Steam Pasteurizer & Sterilizer and Roasting Unit, Food Safety & Quality Solutions, Fruits Processing Machines, Machines and Systems for Traditional and Gluten Free Pasta, Rice Flour Processing Compact Unit, VFFS Packaging Machine, Labelling Technologies from the consortium of world class organizations from various countries like: Italy, Belgium, The Netherlands, Czech Republic, France, Thailand and more.
MISSION
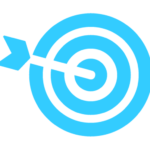
Our passion is to provide world class technology and solutions to our patrons to build brands, win markets and establish a business that ultimately enhances end users prosperity.
To become the company of first choice in our chosen areas by building up beneficial and lasting relationship with customers through a process of continuous improvement.
Jeevika Food Machinery Co., will confidently become one of the most successful company in our competitive marketplace through a unified commitments to the values of:
- Customer Satisfaction
- Continuous Improvement
- Superior Product Quality
VISION
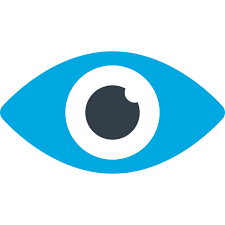
A. Innovative Sorting Solutions from The Netherlands
B. Steam Pasteurizer & Sterilizer and Roasting Unit from France
C. Food Safety & Quality Solutions from Italy
D. Fruits Processing Machines from Italy
E. Complete Systems for Pasta Production for Traditional and Gluten Free Pasta from Italy
F. Rice Flour Processing Compact Unit from Thailand
G. Solutions for the Storage, Dosing and Blending of Ingredients from Italy
H. Fastest VFFS Packaging Machine for Snacks & Candies from Czech Republic
I. Advanced Labelling Technologies from Italy
3U Vision is a young company but with unparalleled experience management. Antonio Uzzo, current Owner and Managing Director, was the owner of SEA, the largest Italian company of the sector, then merged into the Danish multinational CIMBRIA for which he held the role of CEO until December 2018 with extraordinary results. The constant search for innovative technological solutions led him in 2019 to create a team of excellence and found 3U VISION with the aim of rede_ning the quality standards of the optical sector once again.
We aim to create a technology that has the ability to capture even the smallest detail, to improve nutrition, health and the environment in which we live. FENIX optical sorter is the combination result of 40 years experience in vision systems and the latest technologies, in some cases developed exclusively by 3U VISION SRL, Imola, Italy.
FENIX is the _rst 4 colour single camera optical sorter. It is also available with an additional 3 wave length SWIR (InGaAs) patent pending system to _gure out all the problems of the selection: from the color to the foreign bodies, from the shape to the transparency, up to the dimensions.
OptiServe was able to take its plans for a better sorting machine forward. Through the expertise of the University of Wageningen (WUR Food & BioBased Research) combined with the practical experience of OptiServe, we created a machine that could do everything that an ordinary sorting machine couldn’t do.
The sorting machines of that time had limited functions and numerous problems. After several successful years with the E-Select, OptiServe wished to develop a new machine that could perform even better, with a strong emphasis on sustainability, but also with a view to efficiency and optimised production capacity. The idea was to create a sorting machine with higher capacity, a lower error rate, less waste production and less energy consumption. As an ambitious entrepreneur, OptiServe’s founder Antoine wanted to develop the basic platform for all future applications.
Qcify is at the forefront of this quality control revolution. The demand for more quality control and line monitoring in food processing plants is at an all-time high. Production volumes are steadily going up, which requires more sampling and manpower.
This is where QCIFY comes in — a revolutionary line monitoring and quality control solutions provider founded by an enthusiastic group of industry experts with decades of experience in the fields of machine learning (AI), big data, automation and imaging technology.
At Qcify, we’re transforming quality control in the nuts industry with cutting-edge artificial intelligence (AI) and machine learning (ML) at the core of our processes.
Achieve exceptional food safety and flavor with France’s advanced Steam Pasteurizers, Sterilizers, and Roasting Units, tailored for efficient and hygienic processing.
Industrial food processing equipment
FCD SYSTEM has been present in the food inductry for over a decade now with steam pasteurizers (Steristep, Steristir and roasters (Roastinstep).
Ingredients
500+ different products treated
Steristep
Continuous steam pasteurization. Basic, efficient, easy to clean
BIOMETiC provides innovative food inspection systems and AI-powered sorting and grading solutions that help food and fruit producers achieve the highest standards of safety and quality. Our goal is to add real value by enhancing product quality, streamlining your processes, and strengthening consumer trust in your brand.
Every food product, manufacturer, and company in the food industry has specific characteristics and requirements. We at BIOMETiC know this well.
We are technology leaders in food safety, food quality, and production process optimization control. Our experience has enabled us to identify and overcome significant challenges in these fields.
For over 40 years, we have offered innovative in-line food inspection systems combined with easy-to-use customized solutions. One of them is Mito, the unique 3D X-ray inspection system on the market for the food industries with artificial intelligence.
Find out now how Mito can help you meet the challenges of your food industry – whether it’s safeguarding your brand reputation, eliminating waste, or optimizing your production.
PND srl.
Fruit Processing Machinery
Established in 2000, PND is among the top suppliers of fruit processing machinery in the world, delivering innovative solutions to serve Fresh Cut companies, in addition to the established preserved, frozen and dehydrated ones. In PND range of product you can find peeling, coring and cutting machines for apples, pears, kiwi, oranges, pineapples, melons, watermelons, mangos with manual or automatic feeder, prewashing tank and treatment tank. PND supplies standard machines and designs complete tailor-made systems, constantly investing to improve the quality and performance through a combination of know-how and innovation. PND exports its machines all around the world thanks to a commercial network that has spread out worldwide. More than 400 machines are already placed in Europe, South America, United States, Asia and Australia. Key of our success is a really effective, continuous and fast customer care after purchasing; very important for PND team is to assist the customers before and after the machine purchase.
Pasta Technologies Group (PTG) , located in Italy, specializes in industrial machines and complete systems for pasta production, for traditional and gluten-free pasta, as well as gnocchi, and specializes in all areas of processing, such as cooking, pasteurizing, drying, cooling, instant pasta producing, and sterilizing of packages to extend the shelf-life of the product.
PTG is a well-established and highly dynamic company, oriented to technical development and innovation to guarantee a perfect quality product based on customer requirements. The application of know-how is combined with the state-of-the-art product by using the lastest technology available for the automatic supervision of the line during production, to guarantee the highest quality product and the safest working environment for the operators.
The experience gained by working with the most prestigious food companies has enabled PTG to realize machines which are not only technologically advanced, but also suitable for complete sanitization per the most comprehensive hygienic and sanitary laws.
PTG works with the Customer during each step of the project, proposing novel and innovative methods to fulfil customer needs, to include customized solutions based on specific requirements.. In addition to the project development and realization, PTG personally follows the installation, start-up and operator training and provides after-sale service and support, to include inspection surveys performed by specialized technicians.
MAXTEX, or Maximum Technology, was established in 1996 by Mr. Tripop Boonmuan, the owner and the president of MAXTEX Group.
Maxx-Series is a unique processing solution designed to process rice into native flour by wet-milling method which gives a better quality over other _our making processes, resulting in longer-lasting, finest and best quality flour.
Producing native _our from various kinds of rice through the wet milling method by Rice Flour Processing compact unit Due to the modern advanced technology machinery resulting in a silky white colored flour without a rancid smell and changing the flour’s color with the food preservation system that enables the shelf life for up to two years, while increasing the product quality standard and reducing labor in the production process.
Innovation of rice _our production by wet milling method and compact unit machine. Maxx Series by Maxtex, premium product of Thailand, produces longer lasting & best quality _our form various kinds of rice, resulting better _our than other processing methods with low investment, no additional utility construction and labor required.
Our unique Maxx series compact units (Maxx series capacity 75-250 kg per hour) are specifically designed to cater to smaller scale production line requiring lower volume of input raw material as compared to traditional wet milling method, large scale rice _our production which require higher input volume capacity (minimum 1,000kg) and much larger area with massive M&E installation.
Technosilos offers innovative Ingredients handling systems in Food processing & Mixing facilities.
Our solutions cover areas for intake and storage, conveying, mixing, metering, and weighing of the raw materials in powder and liquid form in Large, medium, and small quantities.
We deliver customers ranging from medium size to large operations with efficient, sustainable, and energy-efficient automated processes.
Storing – Silo discharge systems for the storage of raw materials in large volumes.
Conveying – Conveying and sifting the conveyed materials.
Mixing – Industrial Mixing Technologies for Premix and Ready-mix formulas Mixing, drying, heating, moistening Preparation of powdered, fragile or viscous mixes Mixing and packing in line Sanitary and cleanable design.
Liquid & Fermentations – Process of Liquids and semi-liquids Oils, liquid chocolate Preparation of Creams and Sauces Sponge & Sourdough plants Process tanks for Mixing| Heating | Cooling.
Thermal – Control the temperature of product by cooling the raw material Uniform temperature of the dough by Cooling the _our Heating – drying – cooling of powders Preparation of Sponges and sourdoughs Preparation of Creams, Sauces, Semi-liquids.
Dosing & Tracking – Control and trace all the manufacturing steps and the dosing results Manage recipes and planning Manage allergens Inventory management Compliance with legal and / or company-specific directives Interface with ERP systems MES.
VikingMasek: Future of packaging. Since the foundation of the company in 1964, customer´s satisfaction has been VikingMasek´s highest priority. We achieve this goal by continuously improving the cost e_ectivness and performance of all our machines, as well as focusing on innovation for faster and more e_ective machines and new attractive bag styles. VikingMasek`s machine portfolio makes us a single source for all your needs – from simple VFFS machines, through product handling up to turn-key packaging and processing lines. Whether you are looking for a standard single machine or a customized solution, VikingMasek o_ers packaging equipment tailored to your requirements.
World´s fastest continuous motion vffs machine, with bag width up to 250 (300) mm. Viking Masek´s continuous motion bagmaker Velocity 250 (300) is capable of true production speeds up to 250+ bpm. The unique center mounted filling tube and natural counterbalanced sealing profile are designed to provide vibration free, extremely smooth operation at all speeds. Our color graphic operator interface coupled with “o_-the-shelf” PLC controls insures industry leading ease-of use and the highest reliability. The Velocity is also extremely versatile, handling package sizes up to 300 mm (12″) wide and multiple package styles.
ALritma – High performance label applicator
The high performance of ALritma series microprocessor-controlled self-adhesive labellers allows them also to be installed in very fast packaging lines.
There are three versions available: S, M and L, for label widths up to 100, 200 and 300 mm, respectively.
Controls
The label applicator is controlled by a powerful microprocessor with a touch screen display. The most frequently used parameters are displayed via intuitive icons which represent the various functions and provide advanced management, relieving the operator of the need to perform complex mechanical adjustments and noticeably speeding up format changes.